My team was funded by a NASA SBIR to integrate tactile feedback into the space gloves, and in the process built the first haptic impedance matcher, a new tool to optimize size, weight, and power in a tactile feedback system. My role was to develop the impedance matcher and perform mechanical design.
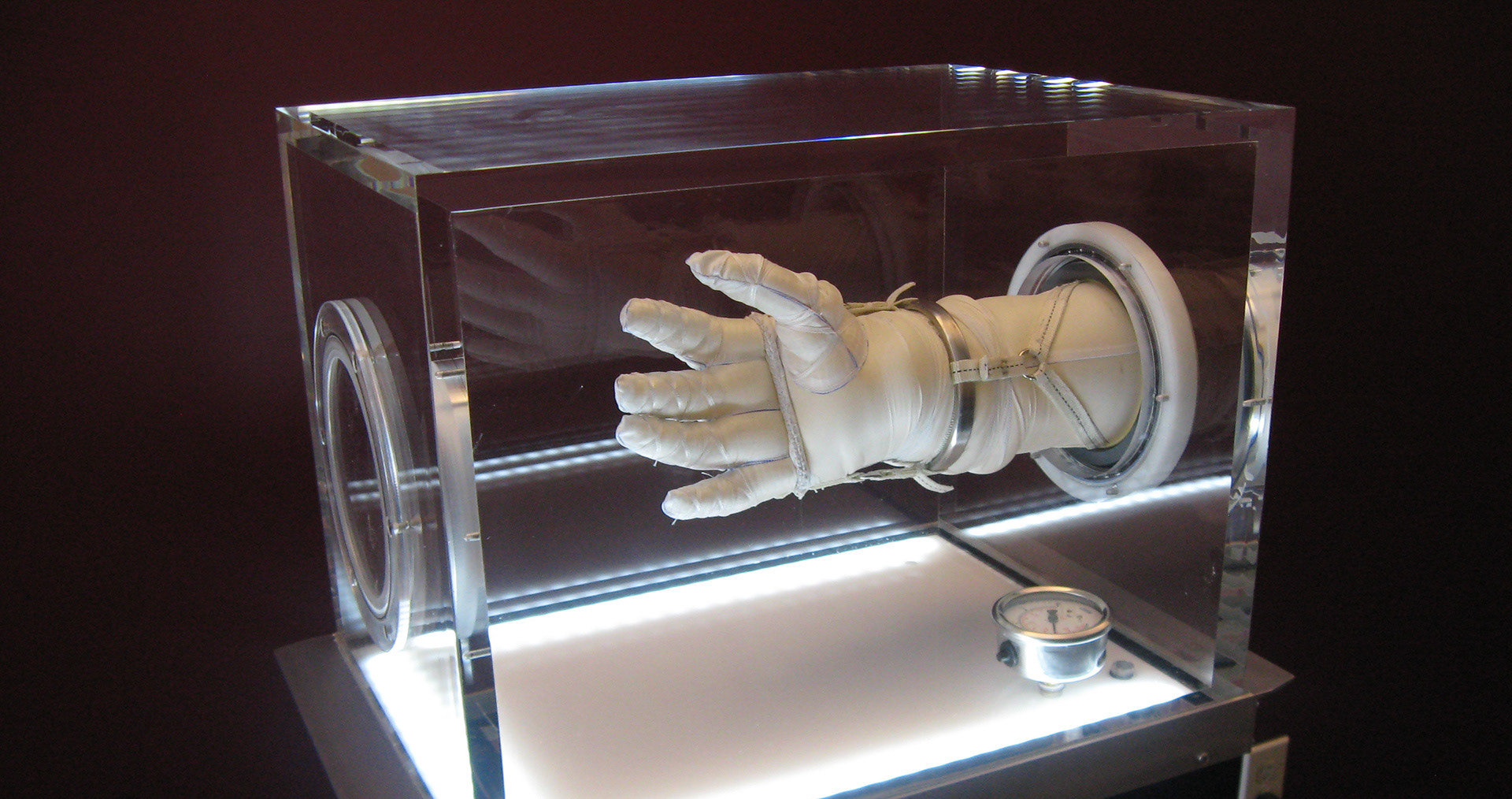
The Flagsuit LLC EVA glove was used as the integration platform for the system
Design
Analytical Modeling / CAD / Prototyping
I helped create the mount and grounding system used to hold the linear resonant actuators and transmit vibrations to the glove. To do this, I designed parts in Solidworks, 3D printed them, and sewed grounding loops onto them.
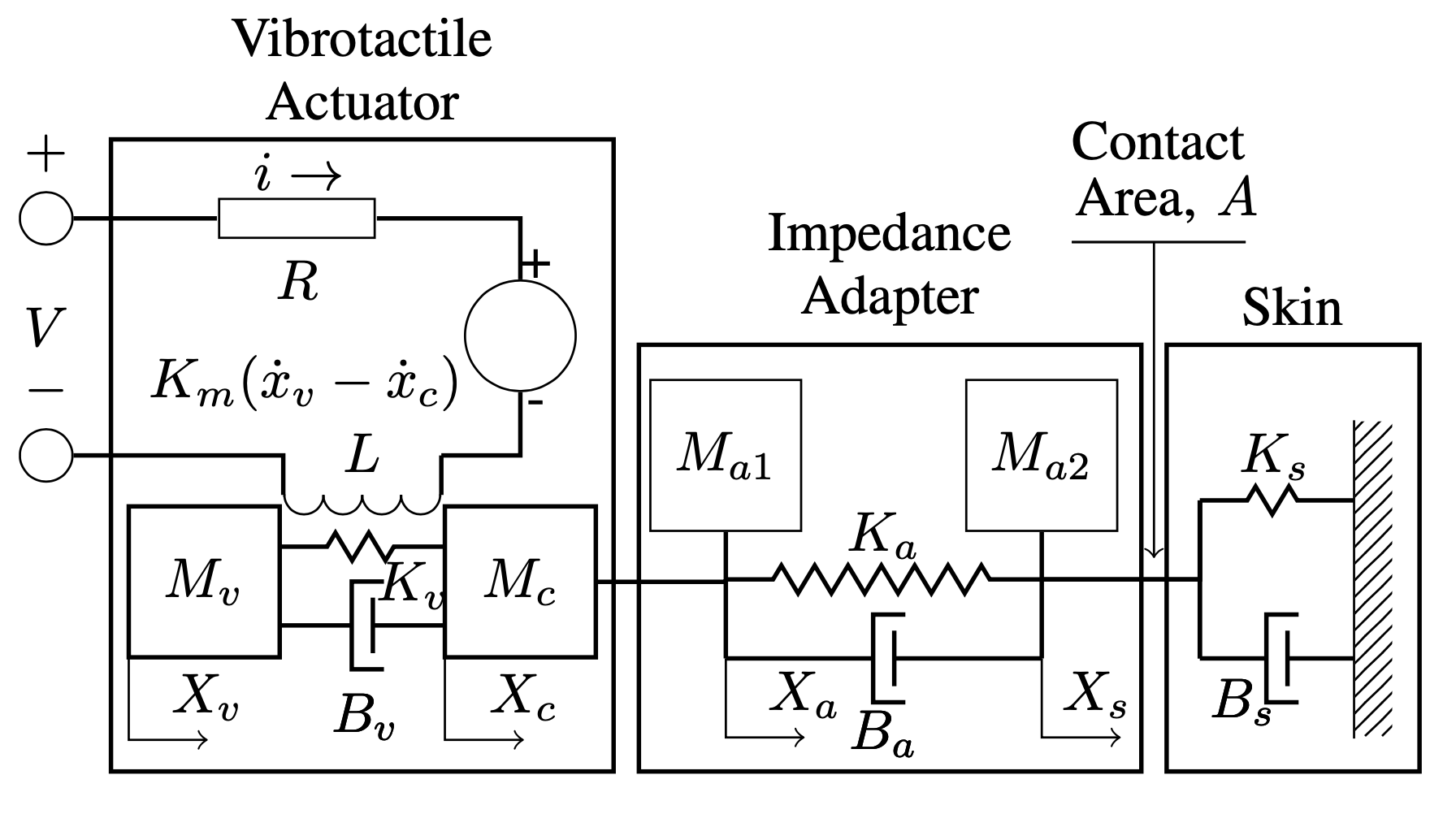
Mechanical model used to optimize the parameters of the Impedance Adapter
Modeling
Mechanical models / Optimization / MATLAB
I constructed a mass-spring-damper model of the system, and synthesized the skin model from a variety of previously published models and data. I found parameters for the impedance adapter by running an optimization in MATLAB, and performed a sensitivity analysis on the result to guide design choices.
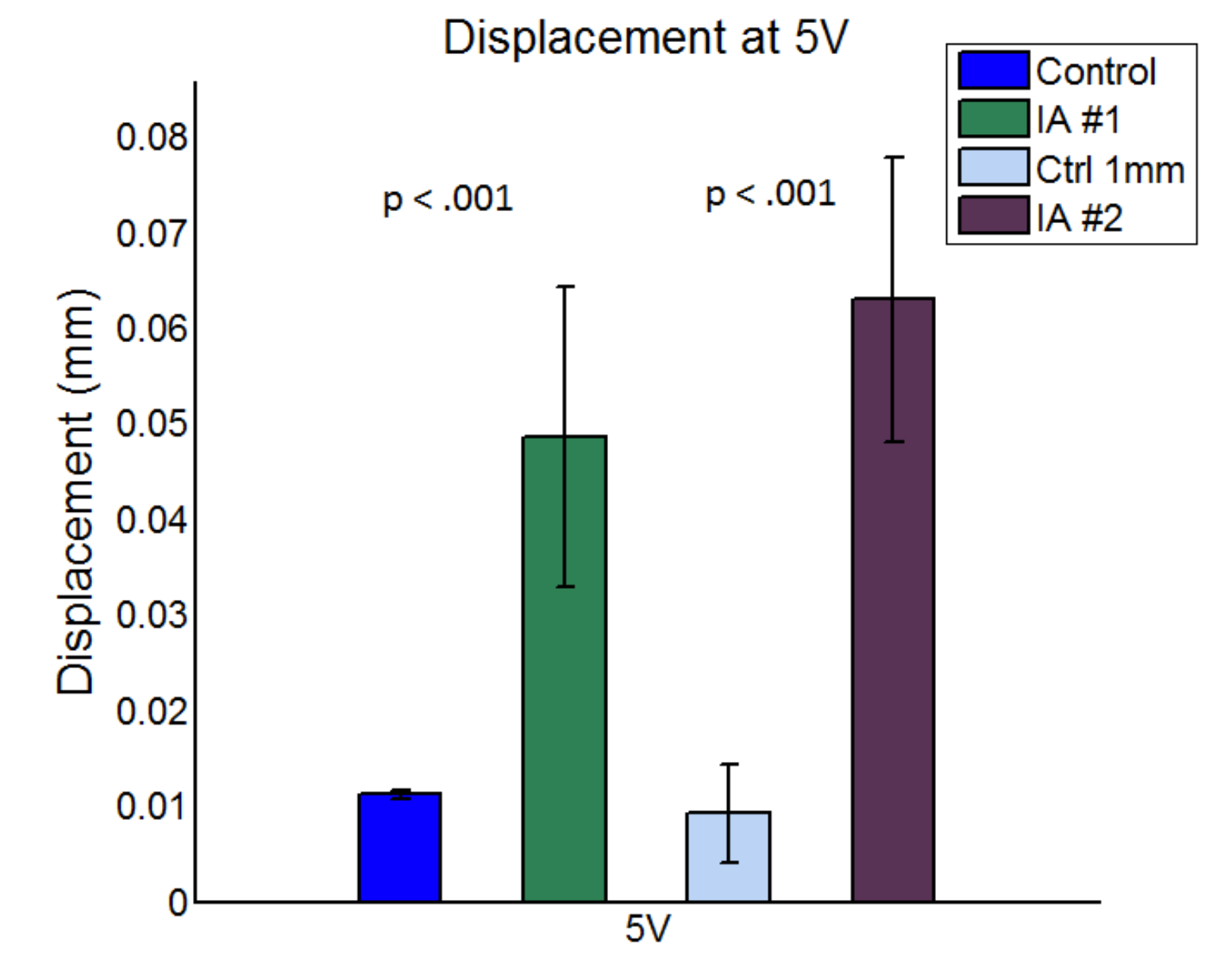
Measurement of the motion of users' skin when vibrated by a vibration motor alone (control) and by a vibration motor coupled to an impedance adapter (IA #1 and #2)
Testing
I designed tests and ran human subject testing to collect objective data and perceptual results. Tests demonstrated a 4x increase in skin vibration with an impedance adapter, closely matching model predictions and approaching optimal energy transfer conditions.
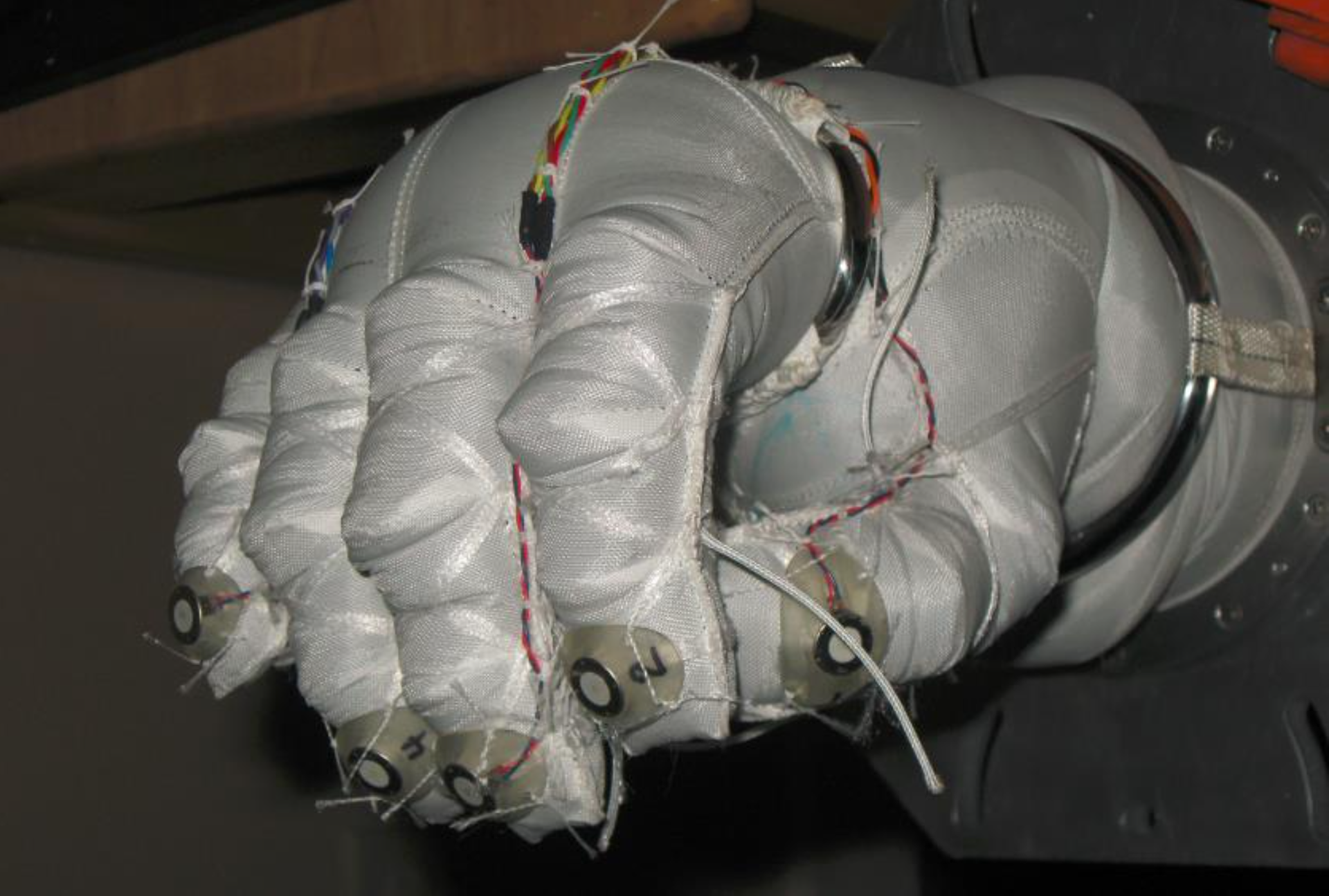
Tactors we built for the project integrated into the Flagsuit space glove
The project delivered a set of space gloves that integrated vibrotactile feedback and hand tracking to be used as part of a augmented reality interface. The system demonstrated 99% accuracy in pressured studies of text entry, and the optimization mechanism demonstrated power reductions of 66%.