Current weather monitoring sensors are either expensive or short-lived. As part of Eltopia, a start-up creating an IoT network for farming, I built a prototype solid-state weather monitoring station that could be manufactured cheaply (under $100) and would last for over 10 years. The key design efforts were around solid-state wind and rain sensors.
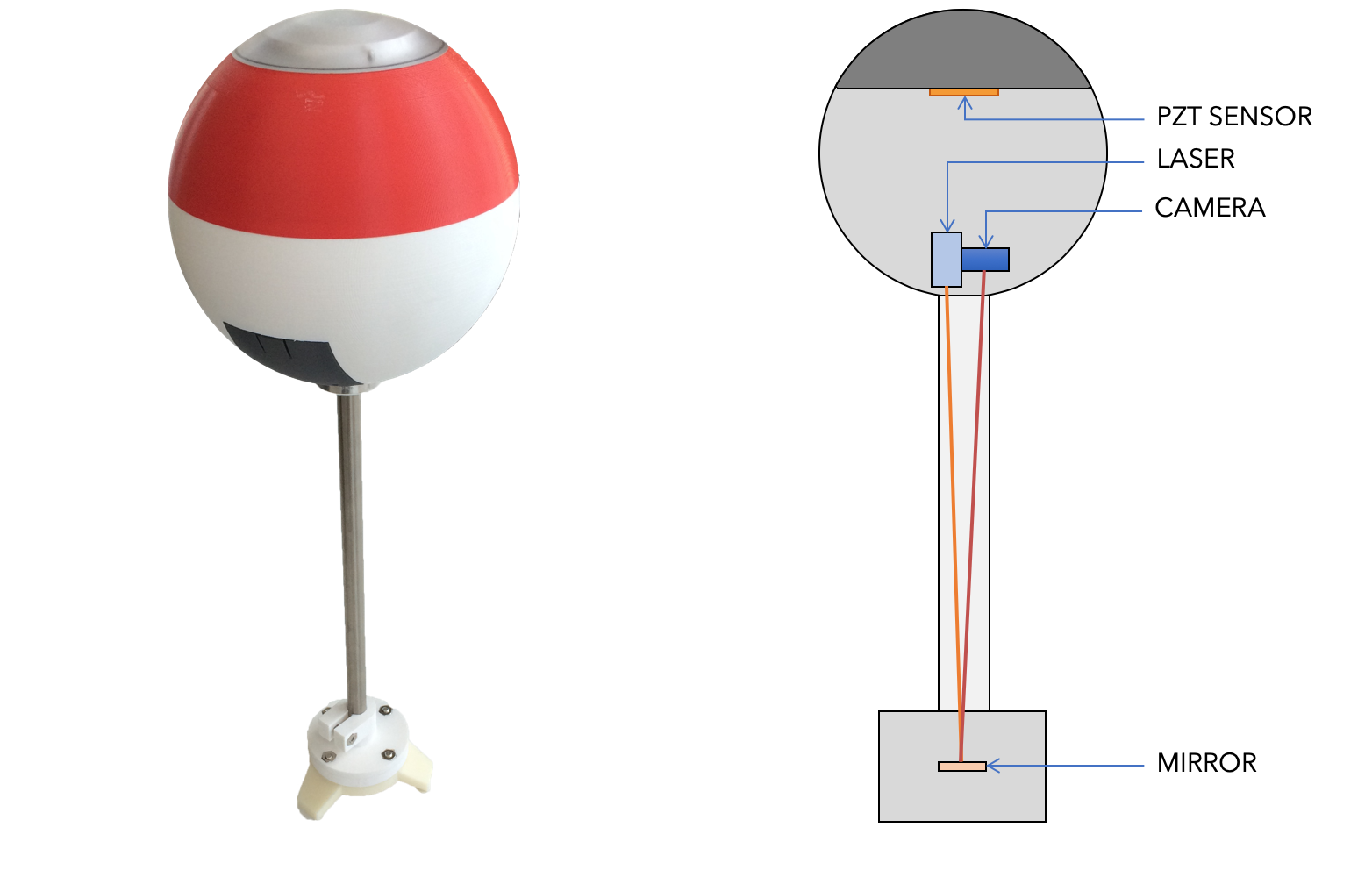
Weather Monitoring Prototype. PZT Sensor responded to vibrations from droplets on the dome, and the Camera tracked lateral deflections of the Laser signal.
Concept
Specification Generation / Trade Space Analysis / System Architecture
Together with the founder, we developed specifications for a weather station designed as part of a farm monitoring network. I researched the range of ground-based weather sensing technologies, and the trade-offs that would need to be made to achieve all or part of the specification. After down-selecting technologies, I led the creation of a system architecture built around an optical sensor for wind and an acoustic sensor for rain.
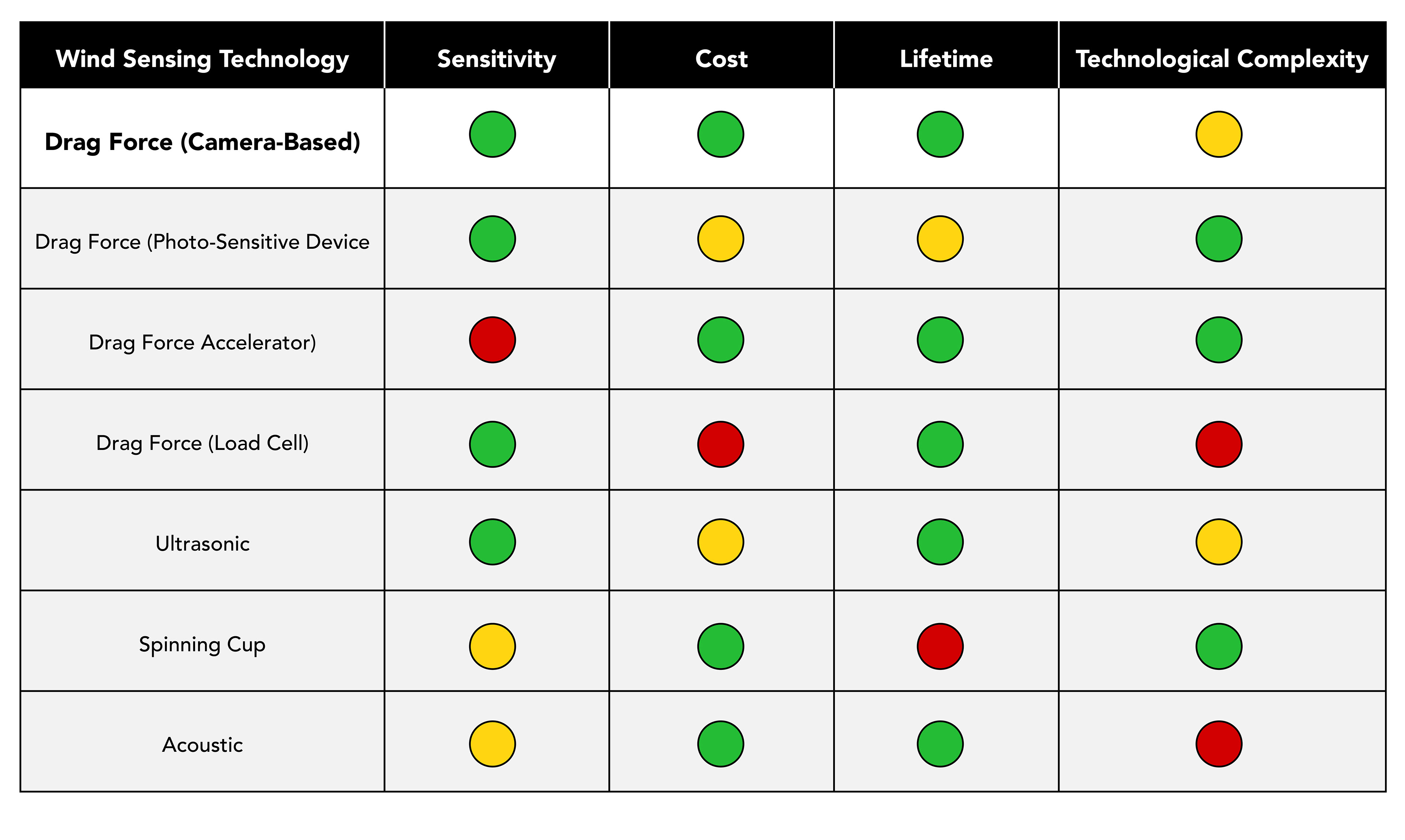
Trade-space matrix for solid-state wind sensing technologies
Design
Analytical Modeling / CAD Modeling / Algorithms / Physical Prototyping
I was responsible for both the system design and the mechanical design of the station. I began by building simple analytical models of the wind sensor from first principles, and used them to guide the design of physical models. The rain sensor relied on the vibration of a dome, and was too complicated to reduce to an analytical model within the scope of the project, so I framed it as an impedance matching problem (coupling rain drops to the dome, and the dome of the piezo) which informed choices about dome material and geometry. 3D modeling was done in Solidworks, and prototypes were built using a 3D printer and parts built by a local machinist.
In addition, I developed the algorithms used to track the position of the laser on the camera, and convert signal on the piezo into rainfall using standard image and signal process techniques coupled with physics-based models of wind and rain.
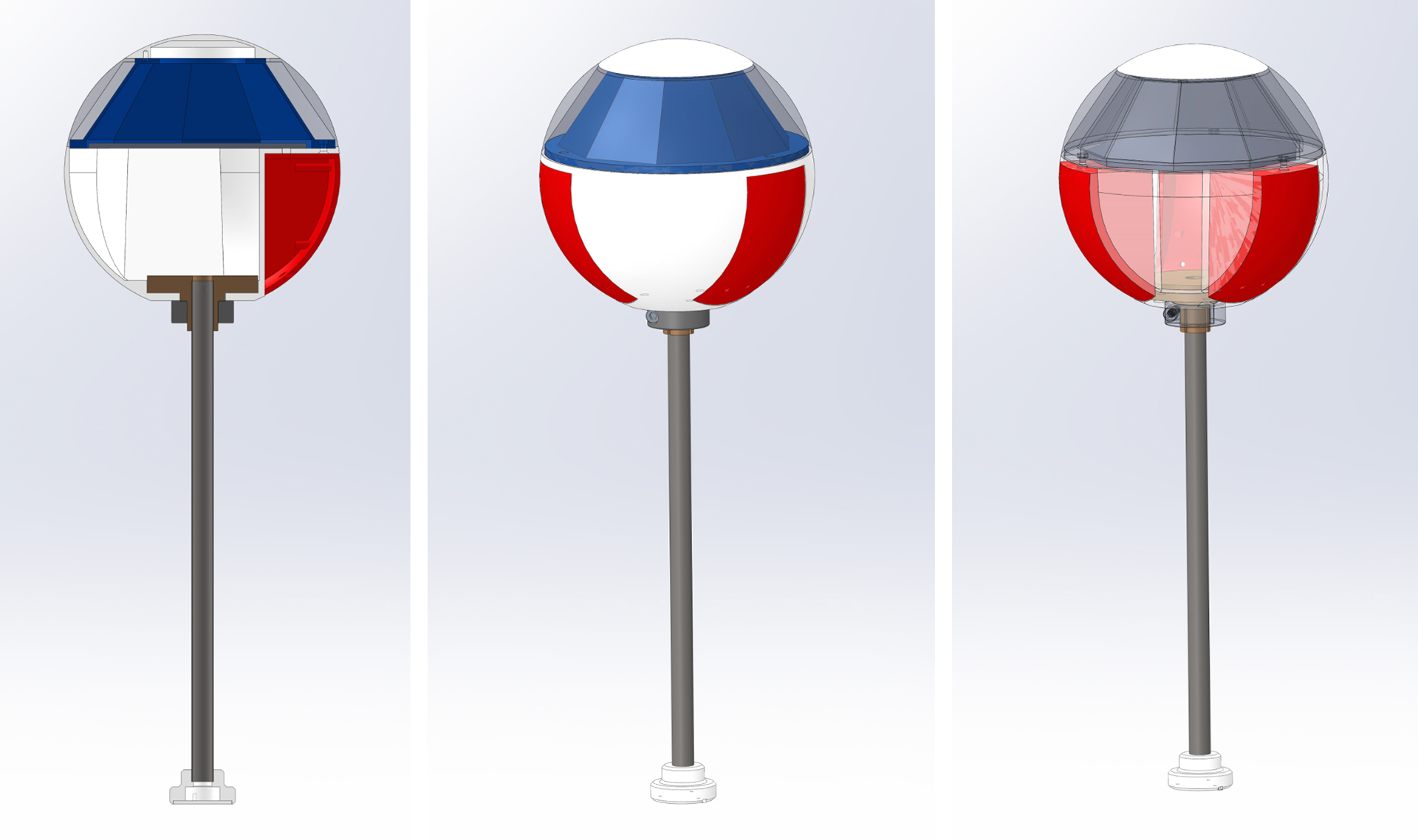
Solidworks models of the mechanical components for the weather station
Validation
Test Systems / Embedded Systems / Data Analysis
I constructed test systems to simulate rain and wind forces and wrote data collection software in LabView, and data analysis scripts in MATLAB. I boot-strapped our test efforts by bringing up an arduino-based embedded system to drive the laser and collect camera data during tests, and wrote a synthetic data pipeline in MATLAB for the image sensor to speed up algorithm development.
The resulting test systems were used to quickly identify problems in prototype designs and validate mathematical models, paving the way to field testing.
LabView code used to capture and segment raindrop signals during bench top tests of the piezo rain sensor
Transition to Manufacturing
DFM + DFA / Materials Selection / Vendor Relationships
Throughout the development process, I built relationships with suppliers for optical components, machined parts, and injection modeling. During the DFM/DFA cycle, I used those relationships to reduce part count by 60% while optimizing parts for molding, machining, and assembly.